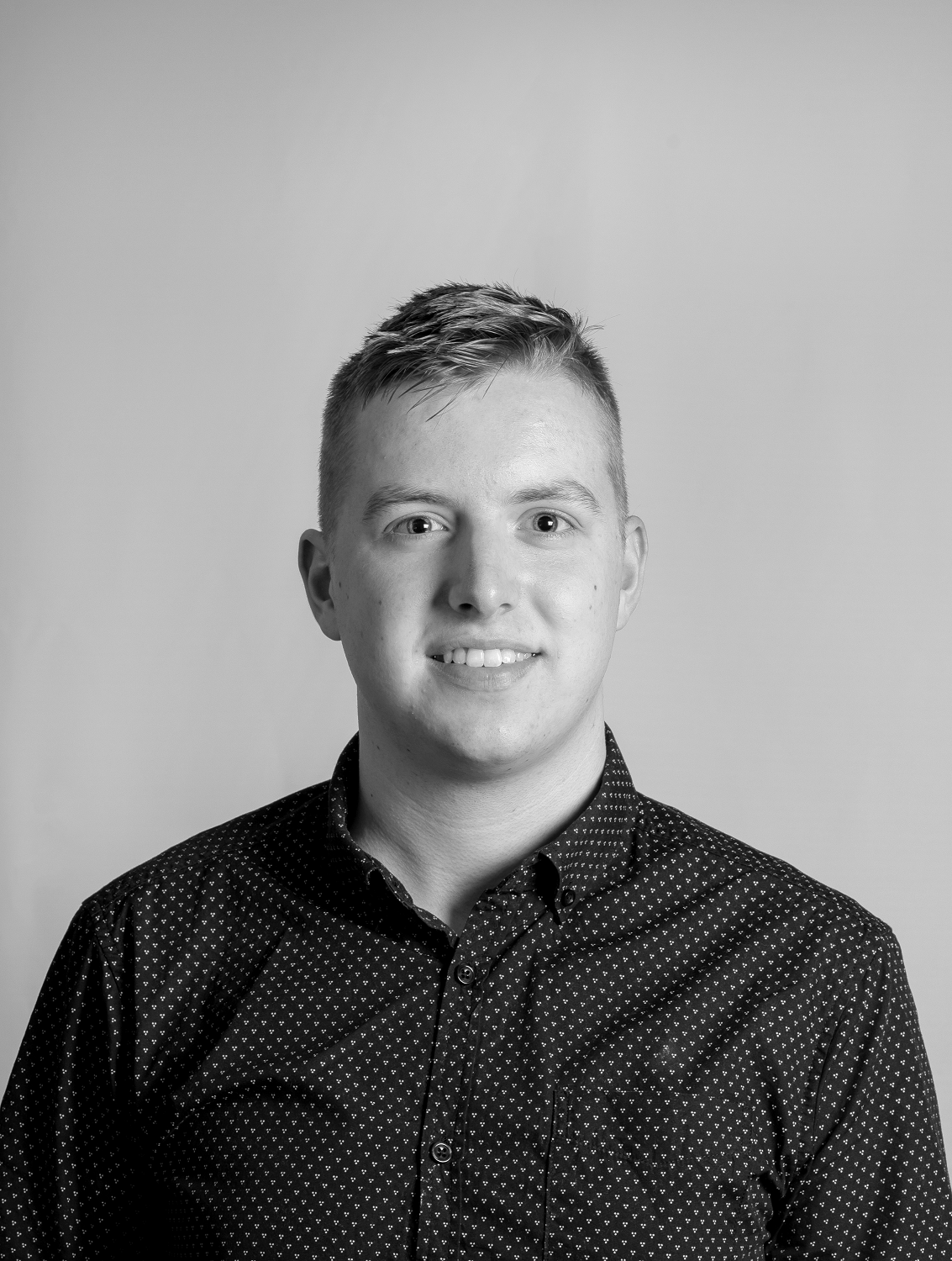
David Judex
My name is David Judex, I'm currently a fourth year Engineering student majoring in Robotics & Mechatronics. Since a young age, I have had a passion for machinery and particularly trains. Studying engineering was a natural choice for me and I have gained much experience in CAD design, additive manufacturing and applying the engineering process to solve real-world problems. I'm keen to expand my skills and gain more experience in engineering industries, particularly aiming for a career within the railway industry.
Optimal Design of a Novel Reduction Gearbox for Robotic Actuators
Within the modern robotics industry, gearbox drives remain a constant area for improvement. A largely unexplored research gap remains to be that of utilising alternate materials, such as plastics, in the design of robotic gearboxes. This gap was chosen as a focus for the proposed design. Using existing design concepts from commercial and experimental examples of planetary-based gearboxes, I designed my own version. The resulting concept was of a self-contained two-stage planetary gearbox. From the initial concept, four design variations were created to gain a comprehensive understanding of how plastics affect the stress performance of gearbox design and to select the most successful design based on the stress levels. The differences between variations were the type of cylindrical gear used (spur, herringbone, and double helical gears) and the face-width of the gears in the design (10-30mm range). Similarly, a cross-section of available plastics were chosen for the comparative analysis, including Acrylonitrile Butadiene Styrene (ABS), Polypropylene (PP), Nylon/Carbon Composite (PA6-CF) and Polylactic Acid (PLA). To validate the design, the bending and contact stresses were primarily analysed and compared between each design-material combination. First through hand calculations followed by a Finite Element Analysis. In the conclusion of this project, it was found overall that the parameters of gearbox design have a larger influence on the stresses involved in a gearbox than the plastic selection. The results indicated that the Spur Gear design of face-width of 30mm was the most successful due to the lower stress involved and the consistency of results. PLA was found to have the highest stress-resistance, although this should not be the sole indicator of a successful material. The performance, operating temperature and design life are other factors that are important in gearbox material selection. These aspects would require further work. An initial prototype of the successful spur-gear design was then 3D-printed at the WSU Makerspace Labs at Kingswood Campus.